Milk pasteurization and cooling unit

Milk pasteurization line based on a plate heat exchanger (pasteurizer), pumps and valves of SPX FLOW APV, as well as components of European brands.
Thanks to the efficiency of the heat exchanger, water and steam savings are ensured. The pasteurizer is controlled in automatic and manual mode. The program is developed by Clever Machines specialists based on individual technological process requirements.
Typical technical specification for a pasteurization and cooling unit
- Product:
- Milk, whey, dairy products
- Number of heat exchanger sections:
- 3-5
- Capacity of Plate pasteurizer:
- 1000 - 40000 l/h.
Advantages of pasteurization and cooling units
-
- End-to-end solution – design, installation, commissioning, customer personnel training and maintenance.
- Increased energy efficiency due to the professional calculation of the heat exchanger and installation configuration. Such solution reduces energy consumption and the cost of production.
- Application of European brands components – SPX FLOW, Siemens, Endress+Hauser, Schneider Electric / Eaton, ABB, etc.
- The use of energy-efficient SPX FLOW APV pumps, the design of which ensures the hygiene of processes and reduces the cavitation risk.
- A set of high-precision temperature visual sensors, pressure and SELI level control.
- Electromagnetic flowmeter "Endress+Hauser" for controlling and maintaining of set parameters.
- Control cabinet with touch–sensitive PLC panel and HMI panel for process control by Weintek / Siemens.
-
- Automation of control, monitoring and error diagnosis process by equipping with the latest generation of APV C4 units. This greatly simplifies maintenance and ensures fault tolerance of the equipment.
- Compliance with sanitary standards, as well as monitoring and compliance with the required indicators.
- СSPX FLOW APV pneumatic valve system with a 5–year drive warranty.
- Option of built-in CIP module provides independence and flexibility of the pasteurizer washing process, which requires careful maintenance compare to other equipment. As a result, the consumption of detergents at the enterprise is reduced.
- Integration into the client's SCADA — increases automation of the pasteurization process, monitoring and archiving of all necessary workflow parameters with data uploading in the desired format.
- Presence of service department and warehouse of consumables for pasteurizers.
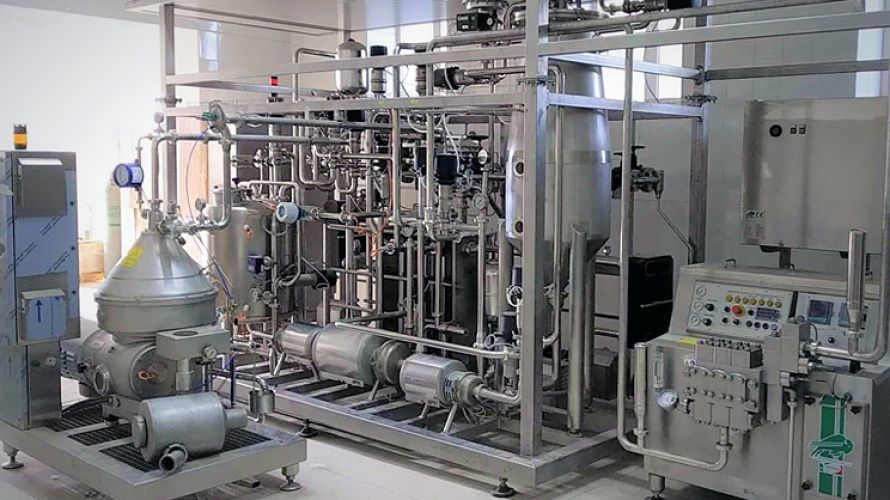
Our engineers will help you choose pasteurization cooling unit for your dairy production – contact us!