They have been widely used in production of:
- whole-milk products: pasteurized, melted and condensed milk, cream of different fat content, milk drinks with fillers, ice cream;
- dairy products: kefir, sour cream, sour cream, yogurt, soft cheeses.
The principle of homogenization
In dairy homogenizers fat and partially protein globules are micronized from the average 4.5-3.5 µm to less than 1 µm. Depending on the product technology, the temperature range of the process is usually being selected between 55 and 85°C. The recommended homogenization pressure depends on the viscosity, density, acidity, fat and dry matter content of the manufactured product. The average pressure range is selected in range between 100 and 300 bar.
Under the microscope: before and after treatment
Non-homogenized product Homogenized product
The result of homogenization is carried out by pushing milk at high speed through narrow slits. The second stage, which in practice has a pressure 4 times lower than the pressure of first stage, makes it possible to exclude the re-formation of agglomerates.
First stage Second stage
In the valve, several forces simultaneously act on the product, which ensure effective micronization of particles:
- strong acceleration with instantaneous braking generates the process of particle destruction;
- intense turbulence and subsequent collision with the "percussion head" experiences the stress of "cut" and hitting the walls;
- hydrodynamic cavitation resulting from pressure reduction generates a high-frequency oscillatory process that participates in the micronization process, making it more qualitative.
Milk homogenizer increases:
- emulsions stabilization and prevention of separation phase;
- homogeneity of the final products and precipitation prevention;
- oxidation resistance, increases the shelf life of the product.
Buy powerful and compact homogenizers of FBF Italia
The Buffalo series are innovative technical solutions focused on improving reliability, convenience and ease of maintenance, as well as reducing operating costs.
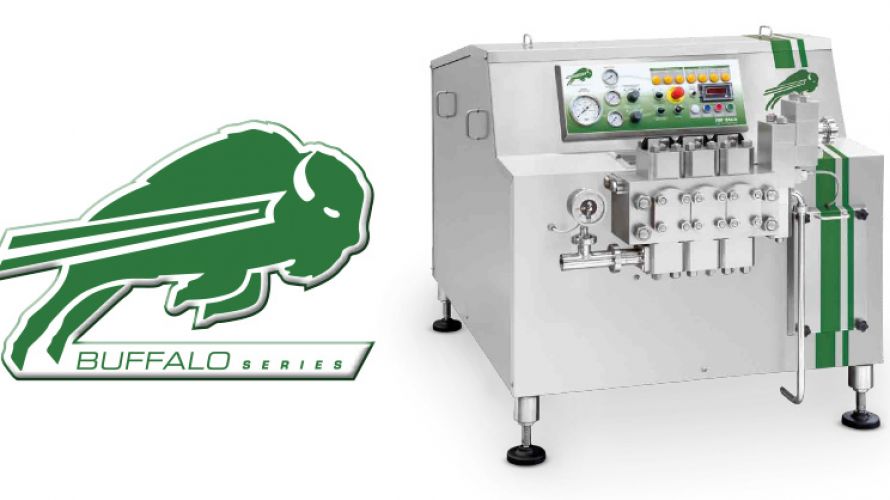
The FBF Italia homogenizer complies with the CE directive, has a capacity from 2,000 to 50,000 l/h, with a pressure of 2,000 bar.
Main features of FBF plunger homogenizers
Compression head
Manufactured as a single block, of SAF (Duplex) 2205 forged steel. The uniquely selected composition of SAF 2205 steels increases strength by an average of 200 MPa, comparing to conventional high-carbon steels. Features:
- mechanical resistance to expansion at temperature fluctuations;
- increased hardness index;
- corrosion resistance in aggressive environments due to high chromium content;
- double ultrasonic flaw detection;
- 5-year factory warranty.
Pumping plungers with Diamond Like Coating
A diamond-like coating gives plungers the hardness of diamond. The friction coefficient is significantly reduced and they are less wearable during temperature fluctuations. A similar coating is used in motors for Formula 1.
- Separate access to each plunger makes maintenance much easier.
- Time savings in terms of consumables replacement is up to 50%
- Replaceable valve group is made of a special wear-resistant material selected for the processed product.
- The safety valve in sanitary version of the spring type is installed on the compression head.
Seat valves
The interchangeable type is designed to be used on both sides, which saves 50% on purchase costs.
Homogenization pressure stability
The regulators control the presence of compressed air and direct the flows to the hydropneumatic unit, directing the hydraulic oil into the homogenization chamber. As a result, stable homogenization quality is ensured, and there is no vibration at high loads during the entire service life of the equipment.
Integrated gearbox
The gearbox-crankshaft connection is a one-piece structure. Advantages are:
- compactness allows you to save space in production;
- less chance of imbalance and vibration;
- crankshaft made of nickel-chromium-molybdenum alloy with nitriding, a technology used in the space industry;
- increased microhardness of the crankshaft, preventing the risk of breakage;
- one type of oil is used for both gearbox and crankshaft.
Energy-efficient four-pole electric motors
- Premium segment motors.
- High quality production.
- Longer lasting
- Less noise and vibration.
Semi-automatic belt tension system
The electric motor is mounted on a self-regulating platform that deviates or stretches to the required level during the natural stretching of belts. No need to constantly check the condition of belts and replace them – minimizing human involvement. Reducing the wear of consumables – belts and gearbox itself.